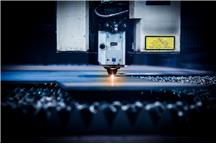
Grupa prof. Ramesha Singha z Indyjskiego Instytutu Technologii w Bombaj wraz kolegami z Uniwersytetu Monash, opracowali model, który uwzględnia zmianę parametrów, jaka zachodzi podczas produkcji części za pomocą technik bezpośredniego osadzania energii, takich jak np. powlekanie laserowe.
Metoda jest szeroko stosowana w konserwacji, naprawie i przeglądzie części i elementów konstrukcyjnych, poprawiając tym samym właściwości materiałowe. Ma to znaczenie m.in. w przemyśle motoryzacyjnym i lotniczym. Prof. Singh wyjaśnia: "Ukierunkowane metody nanoszenia energii mają ogromny potencjał w zakresie naprawy i ponownej produkcji komponentów. Obecność naprężeń resztkowych w osadzonej warstwie zmniejsza jednak trwałość."
Opracowany przez naukowców model pomógł w określeniu krytycznej wysokości osadzania, która zapewnia ściskające naprężenia szczątkowe w zdeponowanej warstwie na poziomie niezmniejszającej trwałości." Odpowiada ona grubości, która po nałożeniu maksymalizuje korzystne naprężenie zarówno w osadzonej warstwie i podłożu. Grubość mniejsza od krytycznej wysokości mogłaby spowodować uszkodzenia na granicy faz, podczas gdy większa grubość, powodowałoby nadmierne rozcieńczenie.
Dzięki opracowanemu modelowi można obliczyć pozycję, w jakiej ma się znajdować laser, aby maksymalizować korzystne naprężenia. Autorzy sugerują, że opracowane przez nich rozwiązanie poprawi jakość, bezpieczeństwo i wydajność komponentów za pomocą powlekania laserowego.
(KB)
Kategoria wiadomości:
Nowinki techniczne
- Źródło:
- 3ders.org; 3dprintingindustry.com

Komentarze (0)
Czytaj także
-
FANUCI – optymalne rozwiązanie do manualnego spawania laserowego
FANUCI jest marką własną firmy Centrum Maszyn CNC. Dzięki wieloletniemu doświadczeniu i współpracy z liczącymi się producentami z branży...
-
Kluczowa rola wycinarek laserowych w obróbce metali
www.automatyka.plWycinarki laserowe zrewolucjonizowały przemysł obróbki metali, oferując niezwykłą precyzję i efektywność. Dowiedz się, dlaczego są one...
-
-
-
-
-
-